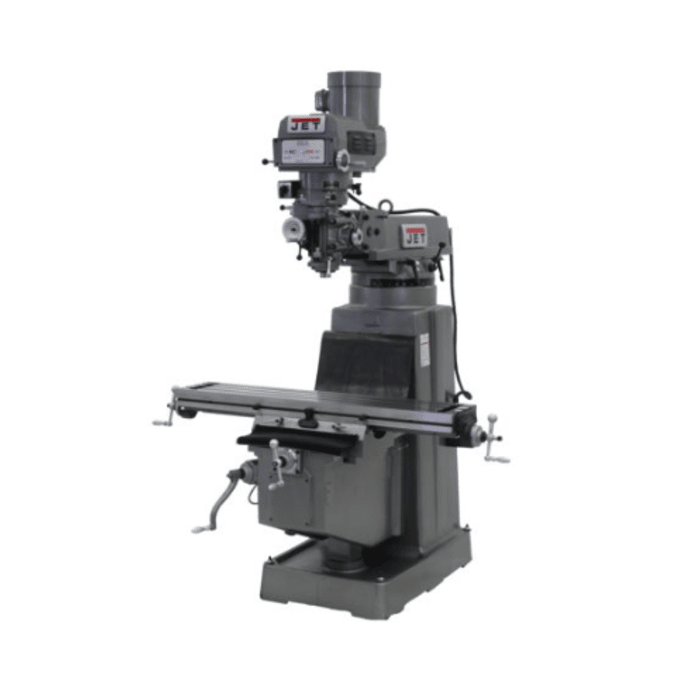
Quick Summary:
Price: $18,829.00
SKU: 691205
Pros:
- Advanced CNC System with the Newall NMS800 DRO
- Certified Meehanite® castings and heavy-duty design offer durability and long-term reliability
- Automatic lubrication system
- X-Axis Powerfeed
- Adjustable spindle speeds
Cons:
- Coolant Pump Not Included
- Quite large and heavy
Personal Experience with the JET JTM-1050VS2 Mill
Having operated various milling machines over the years, my expectations were cautiously optimistic when our shop acquired the JET JTM-1050VS2. From the outset, it was apparent that JET had put considerable thought into the design and functionality of this model.
Ease of Setup and Operation
The setup was straightforward. Integrating the JET JTM-1050VS2 Mill with Newall NMS800 DRO & X-Axis Powerfeed into our workflow was seamless, thanks to its compatibility with our existing tooling and the intuitive layout of controls. The Newall NMS800 DRO was a significant upgrade over our previous machines. Its accuracy and reliability in readouts made a noticeable difference in our precision tasks right from the start. The digital display is clear, even in the less-than-ideal lighting conditions of a bustling workshop.
Daily Operations and Reliability
On a daily basis, the mill's power and stability stand out. The Meehanite® castings and the hardened, ground table provide a stable, vibration-resistant milling environment, which is crucial for achieving precise cuts. The variable speed settings are a boon, allowing us to adjust quickly between different materials and milling needs without hassle.
The X-Axis Powerfeed is particularly useful for longer cuts, reducing manual effort and enhancing the consistency of our output. This feature alone has improved our operational efficiency, allowing the operator to focus more on the precision of the work rather than the physical movement of the table.
Maintenance and Support
Maintenance has been minimal, which is a testament to the machine's build quality. The one-shot lubrication system is a feature that I personally appreciate—it simplifies the maintenance routine considerably. Regular upkeep is straightforward, primarily involving standard checks and the occasional grease application, thanks to this system.
Support from JET has been solid. We haven't needed much, but it's reassuring to know that assistance and parts are just a phone call away, especially with the network of authorized service centers across the country.
Real-World Applications
In terms of applications, the JET JTM-1050VS2 has handled everything we've thrown at it—from standard metal pieces for automotive parts to more complex custom fabrications that require precise detailing. Its ability to maintain precision over long operational hours without drift is a significant advantage for a high-output shop like ours.
Comprehensive Use and Versatility
The true test of any milling machine is its adaptability to the varied demands of daily operations. Over the past several months, I've had the opportunity to push the JET JTM-1050VS2 through a series of challenging projects. Each project highlighted a different aspect of the machine's capabilities.
For instance, working with tougher alloys, which had been a challenge with our previous equipment, became far more manageable with the JTM-1050VS2. The power and precision of the spindle, coupled with the robust motor, allowed us to handle materials like stainless steel and titanium with relative ease. Adjusting the spindle speed to match the material hardness and cutting requirements is intuitive, and the results are consistently precise cuts with smooth finishes.
Handling Complex Projects
One particularly challenging project involved creating a series of intricate components for a custom aerospace assembly. Each component required high precision to ensure they fit perfectly in the assembly with tight tolerances. The chromed quill and the precise downfeed rates allowed us to achieve these tolerances, and the satin chrome-finished dials provided the fine control needed for such detailed work.
This project also made extensive use of the machine's head tilt and ram travel features. Being able to adjust the head for angled cuts without compromising stability or precision was invaluable, especially when working on components that had complex geometries. The ability to maneuver the table extensively along its axes without losing alignment was equally crucial.
Day-to-Day Reliability and Performance
On a day-to-day basis, the reliability of the JTM-1050VS2 has proven itself time and again. For regular tasks like routine part production, which forms the bulk of our work, the mill operates with a kind of "set it and forget it" reliability. We set up our runs, dial in the specs, and the machine delivers, run after run, with minimal intervention.
This consistency is not just about the mechanical design but also about the integrated technologies like the Newall NMS800 DRO, which ensures that even the slightest deviation from the desired settings is immediately noticeable and correctable. This high level of control has minimized our error rates and material wastage, contributing significantly to our operational efficiency.
Long-Term Durability and Minimal Maintenance
Long-term, the durability of the JTM-1050VS2 has been impressive. Despite the heavy use and varied applications it has been subjected to, wear and tear on key components like the table surface and the lead screws have been minimal. This is a testament to the quality of the materials used—Meehanite castings, hardened and ground tables, and chrome lead screws.
The machine's one-shot lubrication system continues to be a standout feature. It significantly simplifies the maintenance process, ensuring that all necessary points are lubricated with just one action, which is especially beneficial during back-to-back project runs.
Beaver Industrial Supply
Purchasing the JET JTM-1050VS2 from Beaver Industrial Supply was an exceptionally positive experience. From the onset, their customer service was outstanding—knowledgeable and responsive, they helped clarify the specifications and capabilities of the machine to ensure it was the right fit for our needs. The ordering process was seamless, with transparent communication at every step, from payment to delivery. The machine arrived on schedule and in perfect condition, thanks to the meticulous care taken in packaging and shipping. The after-sales support provided by Beaver Industrial Supply has also been commendable, ensuring that any follow-up questions were promptly and thoroughly addressed. Their professionalism and dedication made the entire purchase process not just hassle-free, but genuinely reassuring.
The JET JTM-1050VS2 Mill with Newall NMS800 DRO & X-Axis Powerfeed in Detail
When it comes to precision milling in the world of manufacturing, the right equipment is the linchpin of impeccable output. The JET JTM-1050VS2 Mill, equipped with the Newall NMS800 Digital Readout (DRO) and an X-Axis Powerfeed, is a testament to this principle, offering robust features that cater to both high precision and ease of use. In this review, we will delve deep into the capabilities, design, and performance of this milling machine, giving potential buyers a comprehensive overview.
Build Quality and Design
The JET JTM-1050VS2 stands out with its sturdy construction, employing Meehanite® castings known for their durability and minimal stress deformation. The 10” x 50” table is both hardened and ground, providing a solid, flat surface necessary for precise milling operations. The use of high precision class 7 spindle bearings ensures that the spindle runs smoothly under load, enhancing the overall milling accuracy.
One of the most impressive aspects of this mill is its milling head. Precision bored and honed, it promises superior quality cuts—a critical factor for any machining task. Complementing this is the large diameter quill, which is chromed for added resistance against wear and corrosion, a subtle but valuable feature in prolonging the machine's life.
Performance Features
The JTM-1050VS2 excels in its operational features. The three-stage power downfeed with automatic stop is particularly beneficial for tasks requiring consistency and repeatability, which are commonplace in industrial settings. The machine also includes a spindle head that is internally cooled, preventing overheating during extended use.
Speed is variable, ranging from 70 to 3,800 RPM, accommodating various materials and milling requirements. The inclusion of chrome lead screws on the X and Y axes, along with Turcite B coatings, ensures smooth and precise movements, thereby reducing the effort needed to achieve accurate cuts.
Ease of Use
Ease of use is where the Newall NMS800 DRO comes into play, providing clear and precise digital readouts that aid in fine-tuning the milling processes. The X-axis powerfeed further enhances the machine's usability by automating the longitudinal movements of the table, reducing manual labor and improving the consistency of the machining process.
The machine's one-shot lubrication system simplifies maintenance, ensuring that all moving parts are properly lubricated with just a single action, significantly reducing downtime and the risk of wear.
Additional Features and Specifications
The JTM-1050VS2 is not short on additional features. It includes a heavy-duty motor drive and a spindle brake, essential for rapid stops and reducing the time between cuts. The quill feed is triply geared for a variety of downfeed rates, and the machine includes locks on all movable surfaces to secure settings during operation.
In terms of specifications, this mill supports a spindle taper of R-8, has a table size of 10 x 50 inches, and a maximum spindle to table distance of 19 inches. These dimensions and capabilities make it versatile enough to handle a wide range of workpieces and operations.
Advanced Technological Integration
The JET JTM-1050VS2 not only boasts robust physical features but also integrates advanced technology that enhances its functionality and user experience. The Newall NMS800 Digital Readout (DRO) is a prime example of this, offering high precision measurements that facilitate meticulous machining tasks. This DRO is well-regarded for its reliability in harsh working conditions, ensuring accuracy remains uncompromised by environmental factors like dust, coolant, or vibrations.
The machine’s electrical components are designed for efficiency and safety. The no-fuse breaker power connection enhances reliability, reducing downtime due to electrical faults. This feature is crucial in maintaining continuous operation in industrial settings, where productivity hinges on the seamless functioning of machinery.
Customization and Adaptability
One of the more subtle yet valuable aspects of the JET JTM-1050VS2 is its adaptability to various working conditions and requirements. The machine’s head movement can tilt 90 degrees right and left and 45 degrees forward and back, which allows for angled milling operations, crucial for complex shapes and patterns. This flexibility is enhanced by the machine’s large travel ranges, including a 30-inch longitudinal travel and over 20-inch ram travel, making it suitable for larger and more diverse workpieces.
The spindle itself is customizable with a variable speed range, allowing operators to choose the optimal speed based on the material being machined and the specific milling operation being performed. This versatility is crucial for shops that work with a variety of materials and specifications.
Safety and Maintenance
Safety is a paramount concern in any industrial machine, and the JET JTM-1050VS2 addresses this with several built-in safety features. The heavy-duty spindle brake provides an immediate stop to the spindle, allowing for quick responses in case of an emergency. Additionally, the locks on all movable surfaces ensure that there is no unintended movement during operation, which could lead to accidents or errors in machining.
Maintenance is streamlined through features like the one-shot lubrication system, which simplifies the process of maintaining proper lubrication of machine components, thus extending the machine’s lifespan and reliability. The internal coolant tank built into the machine’s base is designed for optional integration with a coolant system, which can help in the reduction of heat and removal of metal shavings during intensive milling operations.
Environmental and Ergonomic Considerations
The design of the JET JTM-1050VS2 also takes into consideration the operator's working environment. The large, easy-to-read dials are finished in satin chrome, which reduces glare and enhances visibility in varied lighting conditions. The ergonomic placement of controls and the smooth operation of the power feeds reduce operator fatigue, which can be a significant factor during long shifts.
Warranty and Support
JET backs this milling machine with their Red Assurance 2-year warranty, underlining the brand's confidence in its durability and performance. The warranty, combined with a network of authorized service centers, ensures that users receive prompt and effective support for any service or repair needs, affirming JET’s commitment to customer satisfaction.
JET JTM-1050VS2 Mill with Newall NMS800 DRO & X-Axis Powerfeed Conclusion
The JET JTM-1050VS2 Mill with Newall NMS800 DRO & X-Axis Powerfeed is a powerhouse that balances complexity and control, making it an excellent choice for professionals seeking a high-performance milling machine. Its robust design, comprehensive features, and supportive warranty make it a valuable investment for any serious machining workshop. This mill is not just a tool but a reliable partner in the precision engineering landscape.
Frequently Asked Questions About the JET JTM-1050VS2 Mill with Newall NMS800 DRO & X-Axis Powerfeed
- What is the spindle taper for the JET JTM-1050VS2 Mill?
- The spindle taper of the JET JTM-1050VS2 Mill is R-8, which is common in many milling machines for its versatility in holding various tools.
- Does the JET JTM-1050VS2 include a coolant system?
- The JET JTM-1050VS2 features an internal coolant tank built into the machine's base, but it does not include a coolant pump, which must be purchased separately.
- What types of materials can I machine with the JET JTM-1050VS2?
- This mill is capable of handling a variety of materials, including metals such as aluminum, steel, and titanium, thanks to its high power and variable speed range.
- What is the maximum distance between the spindle and the table on the JET JTM-1050VS2?
- The maximum distance from the spindle to the table on this model is 19 inches, providing ample space for larger materials and workpieces.
- What are the dimensions and weight of the JET JTM-1050VS2?
- The JET JTM-1050VS2 measures 96 x 78 x 88 inches and weighs approximately 2,900 lbs, making it a substantial piece of machinery requiring adequate space for operation.
- What warranty comes with the JET JTM-1050VS2?
- The machine comes with JET's Red Assurance 2-year warranty, covering service and repairs at authorized service centers across the United States.
Other Variations:
JET JTM-1050VS2 with 3-Axis Newall NMS800 DRO & X Powerfeed 691208 Review
JET 1050VS2 Newall NMS800 DRO X & Y Powerfeeds Review
JET JTM-1050VS2 with Newall NMS800 DRO (Quill), X & Y Powerfeeds 691209 Review
JET JTM-1050EVS/230 690223 Review
JET 1050EVS2/230 Newall NMS800 DRO & X Powerfeed and Air Draw Review
JET JTM-1050VS2 review
Review of JET JTM-1050VS2
Review of JET JTM-1050VS2 Mill with Newall NMS800 DRO & X-Axis Powerfeed
JET JTM-1050VS2 Mill with Newall NMS800 DRO & X-Axis Powerfeed Sale
Review of JET JTM-1050VS2
JET JTM-1050VS2 review
JET JTM-1050VS2 691205 review
Review of JET JTM-1050VS2 691205